Regular engine checks prevent costly failures, maximize lifespan, and ensure peak performance
Regular engine checks prevent costly failures, maximize lifespan, and ensure peak performance
When it comes to heavy machinery, the engine is its beating heart. Whether it's a massive bulldozer, a towering crane, or a sturdy excavator, the engine powers the muscle behind the machine. However, just like any critical component, the engine requires regular inspection and maintenance to ensure it operates efficiently and safely. Neglecting engine inspections can lead to costly repairs, unexpected downtime, and even catastrophic failures. In this article, we'll explore why engine inspections are so crucial for heavy machinery, the key components that need to be checked, and the benefits of a thorough inspection routine.
1. Preventing Catastrophic Failures
One of the most significant reasons for regular engine inspections is to prevent catastrophic failures. Heavy machinery often operates in challenging conditions, where any failure can result in severe consequences, including injuries or fatalities. The engine, being a complex assembly of moving parts, is particularly vulnerable to wear and tear. Without regular inspections, small issues can go unnoticed and escalate into major problems. For instance, a minor oil leak, if left unchecked, can lead to engine overheating and eventually a complete breakdown.
Catastrophic engine failures not only endanger the safety of operators and nearby workers but also result in substantial financial losses. The cost of repairing or replacing a failed engine can be astronomical, not to mention the downtime associated with the repair process. By conducting regular engine inspections, potential problems can be identified early, allowing for timely repairs and avoiding the risk of a complete engine failure.
2. Maximizing Machine Lifespan
Heavy machinery is a significant investment, and maximizing its lifespan is a top priority for any business. The engine is one of the most expensive components of heavy machinery, and its condition directly impacts the overall lifespan of the equipment. Regular engine inspections help ensure that the engine remains in optimal condition, contributing to the longevity of the machine.
During an engine inspection, key components such as the pistons, cylinders, valves, and crankshaft are examined for signs of wear and tear. Identifying issues early, such as worn-out seals or damaged gaskets, allows for timely replacements and prevents further damage. This proactive approach not only extends the life of the engine but also reduces the frequency of major repairs, ultimately saving money in the long run.
3. Ensuring Optimal Performance
The performance of heavy machinery is directly tied to the health of its engine. An engine that is not operating at peak efficiency can lead to reduced power output, increased fuel consumption, and a decrease in overall productivity. For businesses that rely on heavy machinery to complete projects on time, maintaining optimal engine performance is essential.
Regular engine inspections help ensure that all components are functioning as they should. For example, checking the fuel injectors, turbochargers, and air filters can prevent issues such as poor fuel combustion or restricted airflow, which can lead to reduced engine power. By keeping the engine in top condition, heavy machinery can operate at its full potential, delivering the performance needed to meet project deadlines.
4. Reducing Operating Costs
Operating heavy machinery is expensive, with fuel consumption being one of the primary costs. An engine that is not properly maintained can consume more fuel than necessary, leading to increased operating costs. Regular engine inspections help identify issues that can affect fuel efficiency, such as clogged air filters, worn-out spark plugs, or malfunctioning sensors.
By addressing these issues promptly, businesses can reduce fuel consumption and lower their overall operating costs. Additionally, regular inspections can help identify potential problems before they require expensive repairs. For example, replacing a worn-out timing belt during an inspection is far less costly than repairing an engine that has suffered damage due to a broken belt.
5. Compliance with Safety Regulations
Safety is a top priority in any industry that relies on heavy machinery. Regulatory bodies often require businesses to maintain their equipment in a safe and operational condition. Failure to comply with safety regulations can result in fines, legal liabilities, and even the suspension of operations.
Engine inspections are a critical part of maintaining compliance with safety regulations. By ensuring that the engine is operating safely and efficiently, businesses can avoid the risk of accidents and injuries caused by equipment failure. Regular inspections also help maintain accurate maintenance records, which can be crucial for demonstrating compliance during safety audits.
6. Enhancing Resale Value
For businesses that frequently upgrade or replace their heavy machinery, maintaining a high resale value is important. A well-maintained engine is a key factor in determining the resale value of heavy machinery. Potential buyers are more likely to pay a premium for equipment that has been regularly inspected and maintained, as it reduces the risk of purchasing a machine with hidden issues.
Engine inspections play a vital role in maintaining the overall condition of heavy machinery. By keeping detailed records of inspections and repairs, businesses can provide potential buyers with the assurance that the equipment has been well cared for. This not only enhances resale value but also makes the machinery more attractive to buyers.
7. Improving Operator Confidence
The operators of heavy machinery rely on the equipment to perform their jobs safely and efficiently. When operators are confident in the condition of the machinery, they are more likely to work efficiently and with peace of mind. Regular engine inspections help build this confidence by ensuring that the machinery is in good working order.
Knowing that the engine has been thoroughly inspected and maintained allows operators to focus on their tasks without worrying about potential breakdowns or malfunctions. This not only improves productivity but also contributes to a safer work environment, as operators are less likely to take risks when they trust the machinery they are using.
Engine inspections are an essential part of maintaining heavy machinery. From preventing catastrophic failures to maximizing machine lifespan and reducing operating costs, the benefits of regular engine inspections are clear. By prioritizing engine inspections, businesses can ensure the safety of their operations, maintain compliance with regulations, and ultimately protect their investment in heavy machinery. Regular inspections not only keep the engine running smoothly but also contribute to the overall success of the business by keeping projects on track and reducing unexpected downtime.
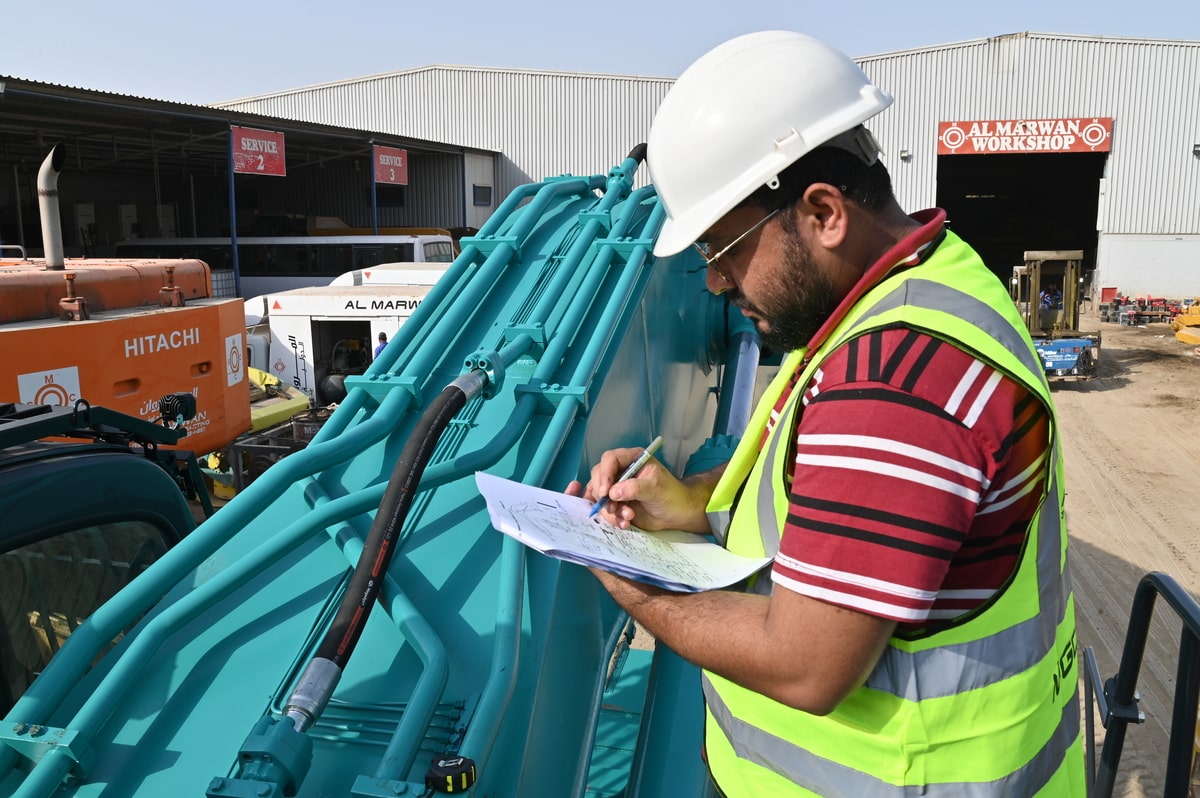